Metal Welders
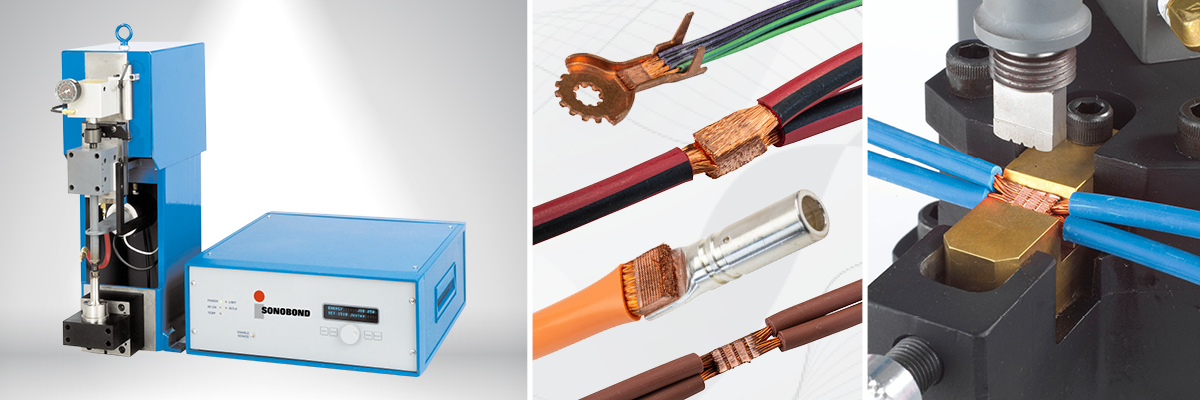
Produce Strong, Precise, Solid-State Metallurgical Bonds
Sonobond’s ultrasonic welders produce strong, precise, solid-state metallurgical bonds without using heat, current or solder. There is no melting or slipping, so you get perfect welds every time. Our systems can also weld tinned copper wires without removing the tin coating.
• Join non-ferrous metals, both similar and dissimilar, with repeated accuracy.
• Join tinned or oxidized metals in a single pulse, eliminating the need for pre-cleaning.
• Join thin-to-thin or thin-to-thick materials.
• Produce joints with excellent thermal and electrical conductivity.
Top Applications for Ultrasonic Welding
• Wire Splicing: Used most commonly for wire harnesses across diverse industries including automotive, marine, and agricultural equipment.
• Spot Welding: Ultrasonic spot welding is used for connecting wires or cables to terminals, ensuring reliable electrical connections that are resistant to stress and vibration. As well as connector to cable assemblies, battery tab to terminal, tabs to solar cells, and bus bar to wire or terminal.
• Wire-to-Terminal: Perfect for lithium-ion batteries, foil-wound capacitors, thin aluminum or copper foil, and electrical contacts.
Click here to download Sonobond’s free Ultrasonic Metal Welding Primer. It contains an in-depth explanation of the process and principles involved in ultrasonic metal welding, as well as helpful information about equipment and applications.
Explore Our Ultrasonic Welding Models
Wire Splicing | |
Spot Welding | |
Wire-to-Terminal |
Sonobond’s Unique “Wedge-Reed” Bonding System
Sonobond’s metal spot welders use the unique, patented “Wedge-Reed” bonding system that combines low vibratory amplitude with high vibratory force for superior weld strength. Shear mode vibration, parallel to the welding surface, ensures dependability while eliminating bending stress. This produces stronger, more durable welds than crimping or soldering, without the porosity or intermetallics of fusion welding.
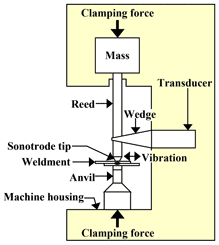