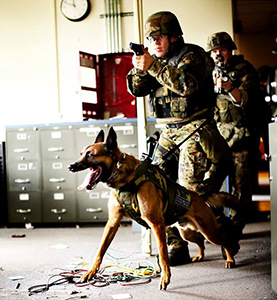
Patrol-Swat vests for worker dogs are assembled with the SeamMaster® High Profile Ultrasonic Sewing Machine to ensure seams in the inner nylon shell are perfectly fused and impervious to moisture.
WEST CHESTER, Pennsylvania, June 21, 2016 – When a Canadian-based manufacturer of protective vests for working dogs sought to guarantee that its canine customers had personal protection comparable to that of their human handlers, it added Sonobond’s SeamMaster® High Profile Ultrasonic Sewing Machine to its manufacturing process.
Now, Patrol-Swat vests produced by K9 Storm, Inc. have secure watertight enclosures for all their ballistic components, exceeding National Institute of Justice wet-conditioning standards that require ballistic vests to be waterproof, even after submersion for 30 minutes (NIJ0101.6). Besides maximum barrier protection, the lightweight, rugged, custom-fitted Kevlar® vests also ensure safe amphibious activities.
“Since bulletproof materials – like Kevlar®, contained in vests – lose their life-saving effectiveness when exposed to water, it’s absolutely critical that the seams in the inner nylon shell are perfectly fused,” says Melissa Alleman, vice president, Sonobond Ultrasonics. “Ultrasonic bonding creates a strong molecular bond that’s impervious to moisture and eliminates stitch holes, glue gaps, fraying and unraveling, substantially reducing any risk of damage to the interior contents of the vest.”
Protection and Mobility for Working Dogs
Highly trained dogs now assist in law enforcement, military, border control and emergency response situations. Whether they are detecting explosives or illicit drugs or helping to find or capture criminals or potential terrorists, they are exposed to increasingly perilous conditions.
K9 Storm, Inc. was established in 1997 by former Winnipeg Police Canine Handler Jim Slater. While he and his police service dog Olaf served in Joint Forces Operations with the Royal Canadian Mounted Police Emergency Response Team, Slater found nothing on the market that could protect Olaf and still allow him the mobility required during encounters with armed and dangerous individuals. So Slater made a custom-fit canine vest using his own ballistic panels, a home sewing machine and his knowledge of working canines.
Utilizing their unique understanding of what working dogs require so they can do their jobs effectively while being properly protected, K9 Storm now produces lightweight, rugged, waterproof tactical gear for dogs employed in security and defense in 24 countries. The canine vests also provide stab protection and feature a built-in harness and load-bearing capabilities to enable the dog to rappel and parachute, as well as remove non-compliant suspects. A built-in platform for camera and communications systems allow the dog’s handler to see what the dog sees and provide instructions, even when the handler is at a distance from his dog.
Ultrasonic Assembly for Canine Vest Production
Prior to learning about Sonobond’s ultrasonic equipment via the Internet, K9 Storm used a single-needle assembly method for its Patrol-Swat vests. The company was convinced to acquire its first ultrasonic sewing machine based on the equipment’s ability to help meet NIJ water submersion standards; the speed and ease-of-use of the equipment; and the friendliness of Sonobond’s staff.
“K9 Storm uses the lightest possible materials when manufacturing the custom-fit K9 Storm Patrol-Swat vests. The Sonobond ultrasonic seaming system is an integral part of the manufacturing process enabling us to achieve watertight ballistic enclosures,” says Jim Slater, president, K9 Storm, Inc. In fact, he anticipates acquiring more Sonobond machines for assembling the company’s products.
Advantages of Ultrasonic Bonding
Ultrasonic bonding occurs when woven or nonwoven materials or blends with a minimum of 60 percent synthetic fibers are placed between the machine’s horn and anvil or, in the case of the SeamMaster, rotating wheel. High-frequency vibrations result in localized heat buildup that causes the synthetic fibers to soften and fuse, creating a durable seal without needles, thread, glue or other consumables.
The versatile SeamMaster® High Profile Ultrasonic Sewing Machine is ideal for sealing the inner nylon shell of body armor systems. Its patented rotary operation bonds and trims synthetic materials in one quick step and its large, high-clearance wheel provides easy access for bulky materials and hand-guided operations. The machine is up to four times faster than conventional sewing machines and 10 times faster than adhesive methods. It has the added advantage of resembling a sewing machine and being easy to operate with only minimal training. The machine also is available as a modular unit that can be integrated into production lines.
“According to some of our customers, their production output levels have increased more than 25 percent since switching from conventional sewing or adhesive machines to ultrasonic assembly,” says Alleman.
No-Cost Ultrasonic Bonding Viability Test
To ensure that its equipment meets manufacturers’ requirements, Sonobond offers a free, no-obligation Ultrasonic Bonding Viability Test. “This enables manufacturers to match our equipment to their specific application and confirm that our products will deliver the quality ultrasonic bonding they need,” says Alleman.
A Track Record of Industry Leadership and Customer Service
Sonobond is a worldwide leader in the application of ultrasonic bonding and welding technology. Over 60 years of operation, it has developed a comprehensive offering of innovative, quality-engineered products. Today, the company manufacturers ultrasonic equipment for leading firms in the aerospace, apparel, appliance, automotive, ballistics, battery, electrical, environmental, filtration, HVAC, medical and solar industries. Additionally, Sonobond employees have earned a reputation for providing exceptional customer service and outstanding technical support before, during and after equipment installation. They’re committed to ensuring that ultrasonic equipment is introduced swiftly and smoothly to any manufacturing operation.
Learn More
For more information on Sonobond’s ultrasonic bonding technology and equipment for protective equipment assembly, or to submit materials for a free Ultrasonic Bonding Viability Test, please click this link. For immediate assistance call 800-323-1269, 610-696-4710, or email Sara Karmilowicz at skarmilowicz@sonobondultrasonics.com. For more information on K9 Storm and its ballistic vests for working dogs, please visit www.k9storm.com or email info@k9storm.com.