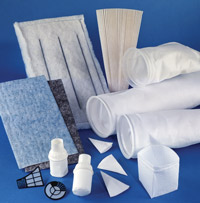
Sonobond Remains the Leading Provider of Ultrasonic Bonders as Filters Made with Synthetic Blends Gain in Usage
WEST CHESTER, Pennsylvania, November 12, 2014 – As synthetic blends continue to penetrate the filtration market, replacing paper and woven materials, the ultrasonic bonding capabilities of Sonobond’s ultrasonic assembly equipment have become even more essential to effective and reliable filter assembly.
The Growth of Synthetic Blends
Woven textiles were initially the first choice for many filtration industry sectors. But by the 1970s, synthetic materials – including blends with polyester, polypropylene, and nylon – and felted filter material proved even more effective for air and liquid filtration products and ideal for ultrasonic assembly.
Today, these materials are gaining in popularity for filtration media used for coolant, vacuum cleaner, HVAC, and liquid applications. New and improved synthetic blends are increasingly used in filters incorporating nanofibers for better dust collection and engine air-intake applications. Plus, their use continues to expand as manufacturers demand energy saving, cost effective, light weight and recyclable materials with finer filtering capabilities; consumers expect better filtration of water and air; and government regulations require higher filtration standards.
Advantages of Ultrasonic Filter Assembly
Sonobond continues to be the leading provider of ultrasonic bonding machinery, offering a reliable, well-established and environmentally friendly technology for assembling filters and filtration products. Sonobond’s equipment employs ultrasonic vibrations to soften and fuse the synthetic blends and filter materials. The ultrasonic bonding process takes only seconds, requires a minimal amount of material at the seam and creates a strong molecular bond that’s impervious to moisture and eliminates stitch holes, glue gaps, fraying and unraveling. In fact, Sonobond’s machines are four times faster than conventional sewing machines and 10 times faster than adhesive machines.
Equipment for Diverse Needs
Sonobond offers a versatile line of ultrasonic bonding equipment to suit the varied assembly requirements of filtration manufacturers. All machines are easy to operate, and require little training.
SeamMaster® Ultrasonic Sewing Machines
Sonobond’s ultrasonic sewing equipment – recently awarded trademark registration as SeamMaster® Ultrasonic Sewing Machines – is among the most flexible and adaptable for filter assembly. Among other applications, the machines are used for assembling air filters employed in HVAC, dust collection, nuclear and bio-chemical applications; for bonding the longitudinal seams of oil containment booms and liquid and gas filter cartridges; for creating fuel filters; and for making filtration components for commercial and military jet fuel handling.
Sonobond’s SeamMaster® Ultrasonic Sewing Machines resemble conventional sewing machines but feature a patented, continuous bonding, rotary operation where both horn and pattern wheel rotate at the same time to cut, trim and sew in one pass, producing an ultra-reliable seal. More than 500 standard pattern wheels are available, as well as custom designs for slitting, sealing, seaming, and embossing.
The ultrasonic sewing machine most useful for filter assembly is Sonobond’s High Profile model, featuring greater clearance for hand-guided operations with tight tolerances and curves. The High Profile model also offers a special fixture for bonding pleated filters with narrow pleats; pleats wider than ½-inch can be welded without a fixture.
RingMaster™ Filter Bag Machine
Sonobond’s RingMaster™ Filter Bag Machine is designed for high-quality, high-volume assembly of heavy-duty filter bags used in a variety of sectors, including the petroleum, food, chemical and pharmaceutical industries. This innovative unit ultrasonically attaches heavy felted filter media to rigid plastic rings, creating a dependable 360-degree bond in just two steps. The process takes less than ten seconds and can produce up to 250 bags per hour. Custom tooling accommodates a variety of bag sizes and ring diameters.
For lower-production assembly, Sonobond’s Filter Collar Bonder™ creates an equally reliable 360-degree weld between a bag and plastic ring in as little as 45 seconds, producing between 50 and 80 bags per hour.
SureWeld™ 20 Ultrasonic PlungeBonder™
For assembling large, multi-layer and difficult-to-bond materials in just one step, Sonobond offers the SureWeld™ 20 Ultrasonic PlungeBonder™, which is ideal for sealing box-style filters and filter bag ends. In addition to producing cube filters, it’s used in the assembly of automotive air filters and HEPA-rated bag-less vacuum cleaner filters.
Free Bonding Viability Test
To ensure that manufacturers use the machine most suitable for their filter media and manufacturing requirements, Sonobond offers a free, no-obligation Ultrasonic Bonding Viability Test. The filtration assembler provides the filter materials and Sonobond creates sample bonds. If the manufacturer decides to install a machine, Sonobond makes certain that work proceeds smoothly and swiftly, providing ongoing technical support and customer service.
For More Information
For immediate information and service, or for instructions regarding submitting materials click here for a free Ultrasonic Bonding Viability Test, phone 800-323-1269 or 610-696-4710, or contact Sara Karmilowicz at skarmilowicz@sonobondultrasonics.com.